At Gentzler Tool & Die, we deliver versatile and reliable line die solutions for manufacturing parts requiring multiple operations. Our process involves using individual dies across multiple stations or presses, ensuring each operation is performed precisely. Whether you need large, complex components or intricate designs, our line die stamping expertise guarantees high-quality results tailored to your needs.
What is a Line Die?
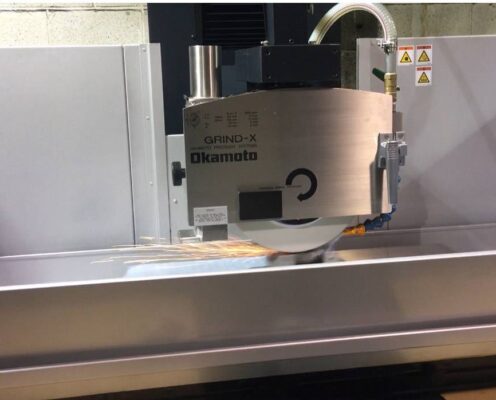
Line Die Process
Here’s how it works:
- Material Loading: A metal blank or sheet is loaded into the first station. Proper alignment ensures that subsequent operations are accurate.
- First Operation: The first line die performs an initial operation, such as cutting the blank into a specific shape.
- Sequential Operations: The part moves through multiple stations, where each line die performs a dedicated task, such as bending, punching, forming, or trimming.
- Completion: After completing all operations, the part is removed from the final station.
- Quality Control: Each part undergoes rigorous inspection to meet the required specifications and tolerances.
Applications of Line Die Solutions
Line die stamping is an essential process for industries requiring complex or large-scale components, including:
- Automotive: Manufacturing structural components like car doors, hoods, and reinforcements that require multiple forming and cutting steps.
- Aerospace: Producing large, precision-engineered parts for aircraft, including wing panels and support structures.
- Construction: Fabricating heavy-duty brackets, plates, and supports used in building and infrastructure projects.
- Energy: Creating parts for power generation equipment and renewable energy systems, such as wind turbines and solar panel mounts.
- Appliances: Manufacturing structural and functional components for washers, dryers, and refrigerators.
Benefits of Line Die Solutions
Choosing line die solutions for your manufacturing needs provides several advantages:
- Flexibility: Line dies can accommodate a wide range of part sizes and geometries, making them ideal for larger components that can’t be processed in progressive or compound dies.
- Precision: Each operation is performed with dedicated tooling, ensuring high accuracy and consistency across all stages of production.
- Customization: The process can be tailored to specific production requirements, such as unique materials or intricate part designs.
- Scalability: Line die setups can handle small-batch and high-volume production, adapting quickly to changing project demands.
- Reduced Material Stress: Sequential operations minimize the stress on materials, preserving their integrity and ensuring better performance in the final product.
How Do Line Dies Differ from Other Dies?
Line dies differ significantly from other die types in their structure and functionality. While progressive and compound dies focus on performing multiple operations in one press stroke or station; line dies spread these operations across multiple stations. This makes line dies particularly effective for:
- Large parts that require complex shaping or cutting.
- Components that demand multiple steps, each requiring precise control.
- Situations where material characteristics, such as thickness or hardness, make it impractical to combine operations.
Progressive Die vs. Other Dies
Contact Us
Are you looking for reliable compound die solutions to enhance your production capabilities? Contact us today to learn how our expertise in precision tooling and efficient manufacturing processes can meet your specific requirements.